Litehouse has been making fine foods for over 60 years. Starting as a family-owned restaurant, Litehouse has now grown significantly from its humble beginnings. The company supplies premium salad dressings all over the country. You’ve tasted them, and you love them!
Each dressing recipe needs to have the dry mixture made before mixing with the wet ingredients. Mixing each batch of dry ingredients one at a time has been the norm for a long time at Litehouse. They were looking to improve the process and prepare larger amounts of dry ingredients ahead of time and have ready when it was time to mix a new batch of dressing. Working with Annik and Marion, two 30 cubic foot paddle mixers were integrated into their facility. This allowed for a large quantity of dry mix to be bagged and prepared to blend in with the wet ingredients, exactly what Litehouse needed to increase their efficiency. Instead of gathering the dry ingredients when it is time to blend a batch of salad dressing, the dry ingredients are ready to go, having been prepared ahead of time in larger quantities.
The solution was built with safety in mind. Two large grates equipped with safety limit switches to ensure that anytime the safety grates are removed from the mixer, the mixing paddles will not run, eliminating the risk of possible injury from the equipment, while allowing easy equipment cleaning daily.
As a result of the improved efficiency, this department of Litehouse Foods was able to adjust their staff scheduling from 7 days to 5 days per week giving the entire department weekends off. Labor costs were reduced significantly and their output increased by 12 percent!
Client Needs: Looking to improve production efficiency and reduce labor costs in the production plant
Products Used: Two Marion 30 cubic foot paddle mixers
Special Features: Advantage of seal disassembly, cleaning and re-installation in less than 5 minutes. Design is ideal for equipment requiring quick and thorough removal and assembly
Results: The new mixers allowed for an substantial increase in efficiency. Staff scheduling changed from 7 days per week to 5 days giving an entire department weekends off. Labor costs were reduced significantly. Output moved up by 12%.
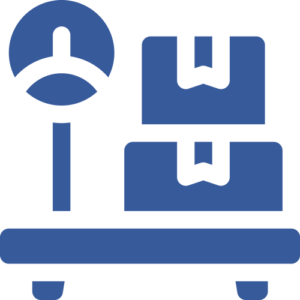
Mix Time: 5-6 Minute Mix Time Per Batch

Duty: 5 Days A Week 10 Hours A Day
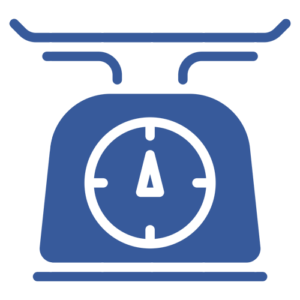